QUALITY AT SANMINA
Lean & Six SigmaContinuous performance improvement is an expectation of any successful company. At Sanmina, our Lean & Six Sigma programs help us meet this expectation.
Continuous performance improvement at Sanmina is driven through Lean and Six Sigma Programs. We recognize that all employees have expertise which can identify specific opportunities for improvement. Using data and quantitative methods for analysis and decision making, we have found that a better understanding of the process drives additional performance improvements.
Plant and Division management teams drive the identification and completion of individual projects, based on specific needs at each plant. In many cases, customer input is part of the project selection process and we drive joint projects with the customers’ teams.We use a shared on-line project database to record project summary and provide links to the detailed project reports. Best practices and lessons learned are key activities driven by Divisional/Regional and Corporate Quality teams. Each year, we complete hundreds of Kaizen events and Six Sigma Projects, often used to share best practices company wide. More importantly, we use our increased awareness of Lean and Six Sigma practices to develop and deploy new manufacturing and administrative processes “right the first time”.
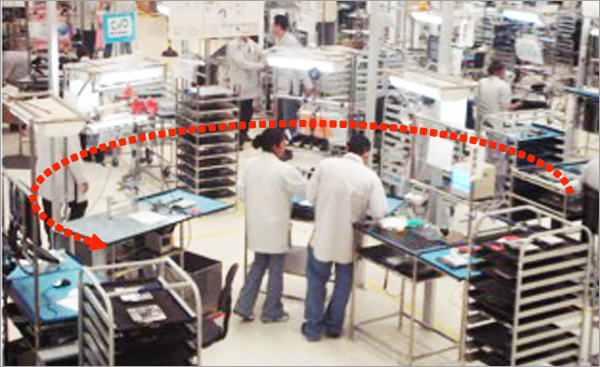
LEAN
Lean is about eliminating all forms of waste. A Lean organization uses less of everything. Benefits of Lean implementation include shortened lead time, improved delivery, capacity and flexibility. Starting with the basic concept of value for our customers, we look for opportunities to improve our process flow and reduce overall effort and cost. Mistake proofing methods are investigated and implemented when new processes are established. Standard work assures all employees fully understand what to do and how to do it. Pull systems can control when work is performed resulting in minimum inventory and potential quality problems.
Common Lean Tools:
- 5S & Visual Management
- Value Stream Mapping
- Set-Up Reduction
- Kanbans & Supermarkets
- Operation Balancing
- Total Productive Maintenance (TPM)
- Manufacturing Cells
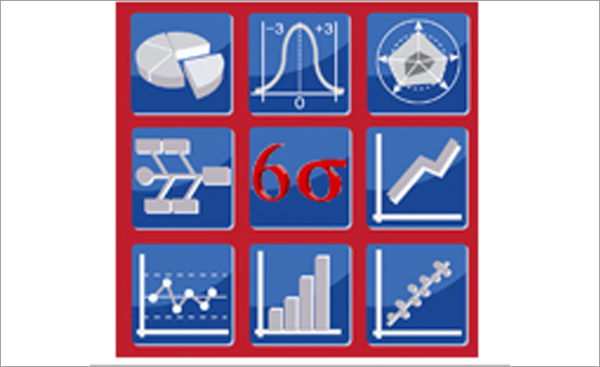
SIX SIGMA
Six Sigma is about reducing variation. This provides improved confidence in the output of our processes. Benefits of Six Sigma implementation include improved yields, improved process capability and effective root cause validation. Six Sigma tools provide a detailed understanding of what contributes to process variation, allowing process inputs to be set at optimal levels. Statistical evaluation of process output can discriminate between expected and unusual process output, further improving process predictability.
Common Six Sigma Tools:
- Process Capability Analysis
- Measurement System Analysis (Gauge R&R)
- Control Charts
- One and Two-Sample Significance Tests
- Analysis of Variance (ANOVA)
- Regression Analysis
- Design of experiments (DOE)
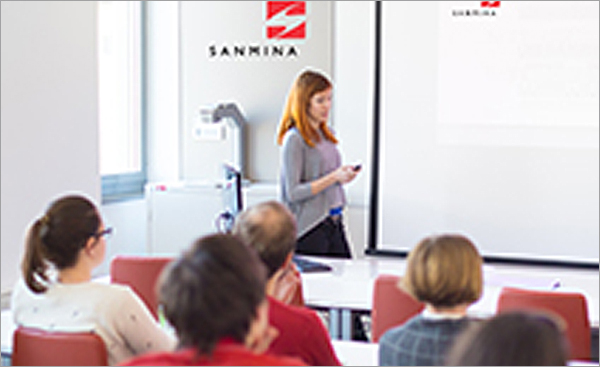
LEAN & SIX SIGMA TRAINING
Lean & Six Sigma training is designed to better prepare people to apply a variety of problem solving and performance improvement tools and to more rapidly identify and implement Lean and Six Sigma projects, providing value to Sanmina and our customers. Training materials and exams are common across the company and are shared by all authorized instructors. All higher training levels include any lower level training levels.
- White Belt – a single training module providing a short overview of the Lean & Six Sigma program at Sanmina.
- Yellow Belt – 10 training modules covering basic Lean and simple problem solving tools.
- Blue Belt (Lean Specialist) – 10 training modules covering additional Lean tools.
- Green Belt – 10 training modules covering simple quantitative (statistical) methods.
- Black Belt – 16 training modules covering more advanced statistical theory and tools.